In the process of producing heat pipes, the shrinking operation is a key step. Its purpose is to increase the density of the filler material (such as MgO powder) inside the pipe, thereby improving thermal efficiency and ensuring the stability of the resistance wire. The shrinking process used to be as follows:
- Pipe Cleaning: Carefully wipe all parts of the pipe to ensure it is free of dust and impurities.
- Direction of Shrinking: Ensure that the solid plug enters the roller first during shrinking. For hollow burn pipes, it is recommended to shrink in both directions.
- Diameter Tolerance Control: After shrinking, the diameter tolerance should be controlled within ±0.08mm, including roundness tolerance.
- Straightness Requirement: The straightness after shrinking should be no more than 4mm per meter.
- Roller Adjustment: Each time the roller is adjusted, the number of test pieces should not exceed 8.
- Quality Inspection: Inspectors should check the diameter and straightness and randomly inspect 20% of the resistance values and pipe lengths.
Note: After shrinking, the difference between the longest and shortest pipes should not exceed 3% of the post-shrink pipe length required by the production order. If the difference in length after shrinking is too large and irreparable, the product will be counted as waste.
Tools and equipment include a shrinking machine, tape measure, and calipers.
In this process, the FUTAI TL-101 Shrinking Machine demonstrates its outstanding performance. The TL-101 is specially designed for reducing round and metal-sheathed tubular heating elements, ensuring a high degree of precision, with a roundness ratio of 1:300 and a flatness of +/-0.05mm. This precision is crucial for ensuring the quality of the heating pipes.
Key features of the TL-101 Shrinking Machine include:
– High Precision and Efficiency: Ensures precise reduction of tubular components, crucial for optimal filling of MgO powder.
– Smooth Continuous Operation: Designed for silent operation and stable performance, providing a smooth, continuous one-step reduction process.
– High Production Capacity: Suitable for high-volume production, quickly adapting to different pipe sizes.
– Automation and Compatibility: Can be used in conjunction with other equipment such as the TL-312 feeding and testing machine, supporting automation of the production line.
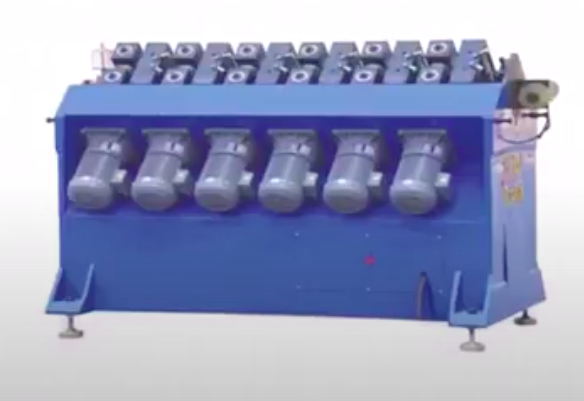
Heat Pipe Shrinking Machine
Therefore, FUTAI’s TL-101 Shrinking Machine not only improves the efficiency and precision of heat pipe processing but also ensures the high-quality standards of the final product, making it an indispensable key equipment in the production of heat pipes.